Challenging Site Conditions: Foundations of a Steel Plant in Brazil
The almost 9 km² factory area comprises two blast furnaces, a coke plant, a sintering plant, converters and casting plants, storage areas for raw materials, including the infrastructure with deep sea port and railway line. A power plant, water and sewage treatment plants as well as various plants for the post-treatment and further treatment of steel slabs and blast furnace slag are added. Prior to the start of construction, the site had to be raised by 1-2 m using 10 million m³ dredged sea sand as filling due to the high risk of flooding. Foundations were a serious challenge as well, with soft organic clay at depths down to 25 m, and sand in loose to dense layers with activated clay lenses. Around 35 m below the original terrain lay granite and gneiss bedrock weathered in the upper few meters. The sand layers contain groundwater with a perched water table reaching up to ground level.
The heavy weight of the buildings and roadways required innovative foundation solutions due to the poor subsoil – keeping within tolerance of potential deformation on soil liable to subsidence proved to be a geotechnical challenge in planning and construction; the load-bearing clay layers would not have stopped deforming for years without the necessary stabilising countermeasures.
From a geotechnical point of view a unique project.
Satisfying these complex requirements required beginning with a building model based on geotechnical field and laboratory experiments. Our earth stability, subsidence and stability calculations resulted in using prefabricated concrete and steel piling as well as in-situ piling for the buildings and plants, and almost the whole gamut of ground improvement methods for compressing, consolidating or replacing the existing soil in storage and operational areas as well as heavy crane sites less sensitive to subsidence. We frequently used sand and stone columns on the base layers, mostly in combination with geopolymer mesh; this phase involved numerical calculations in the design, and previous tests using corresponding field experiments to confirm and monitor the work. Pre-empting subsidence by preloading and drainage elements to speed up consolidation made up an important part of the foundation plan.
Our project team supervised all the foundation work on the major construction site. We used around 2,200 km of piling, 5,000 km of sand and gravel columns, mortared 5,000 m³ of soil, dug 3,500 km of vertical drains into the ground, and moved around 500,000 m³ of preloading material while building the steel plant – a unique project from a geotechnical perspective.
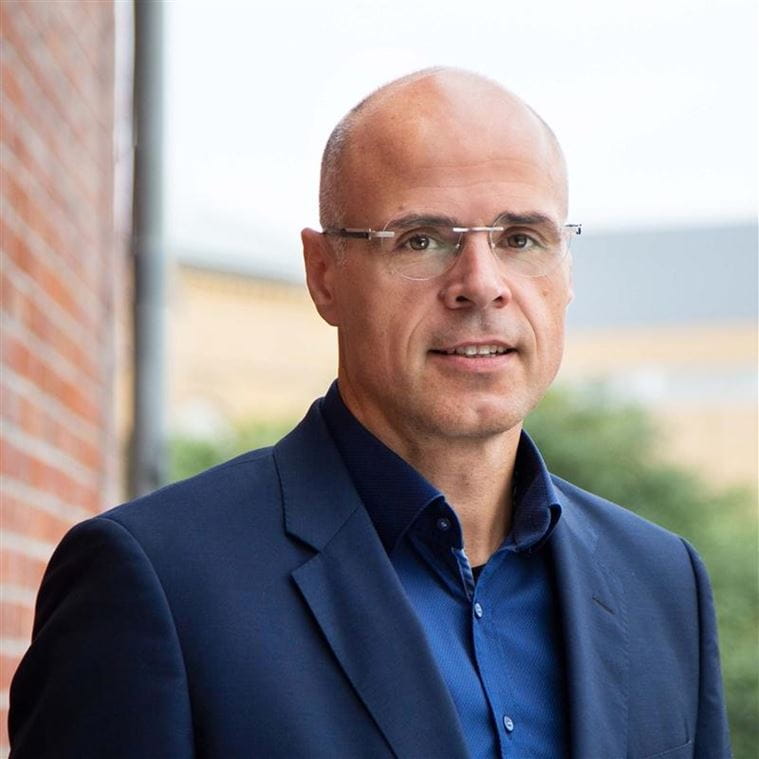
The teamwork of various disciplines and nationalities for a common goal was impressive.