Unlocking Waste Reuse Benefits for Craft Breweries
Mid-sized and large craft breweries face a big obstacle to meeting the growing demand for their beers: high discharge fees for the waste generated by the brewing process. To avoid expensively discharging brewery wastes like hops, yeast and fatty sediment, breweries can use treatment techniques like anaerobic digestion. Not only do these techniques save money, they also have the potential of generating biogas and recycled water. Until now, cost and complexity have deterred most brewers from using these techniques, but the application of new membrane technologies entering the market are making a tastier business case for anaerobic digestion.
CDM Smith’s R&D Program helped fund a pilot study that demonstrated the benefits of one of these technologies, the anaerobic membrane bioreactor (AnMBR). Using an AnMBR for brewery process waste resulted in more effective treatment than industry-leading alternatives, unlocking multiple potential benefits for craft breweries.
Collaborating to Cross a New Frontier
As New Belgium Brewing, one of the nation’s largest craft brewers, eyed expansion from its Fort Collins, Colorado headquarters to the thriving beer scene of Asheville, North Carolina, space constraints challenged the need to treat the brewery wastes that a new facility would generate. CDM Smith engineers believed that an AnMBR treatment system could prove effective by providing excellent resource recovery on a small footprint. AnMBR technology has been used successfully in the dairy industry for similar purposes. Proving that this technology could work with brewery waste meant crossing a new frontier.
“Because AnMBR had not been proven in the brewing industry, New Belgium wanted to fully vet it before committing to it for Asheville,” says CDM Smith discipline leader Tim Rynders, PE. “We proposed funding a pilot-scale R&D study to collaboratively push the limits of these new membranes and to test if AnMBR could provide New Belgium with the right solution.”
GE Water & Process Technologies joined the R&D effort, providing its proprietary membranes in kind for the 9-month study, while New Belgium staff signed up to lead the operations and data collection activities for the pilot.
From Process Waste to Reusable Resource
Brewers have traditionally resisted conventional anaerobic membranes because of fouling issues. “Today’s membrane systems are more refined,” says Rynders. GE’s AnMBR system uses hollow-fiber ultra-filtration membranes submerged inside a process water treatment tank. The process wastewater is constantly pumped through the tank at a higher rate than what is filtered.
“The new membranes can’t help but hold the solids in the digestion system longer, meaning that the methanogens, our preferred ‘bugs’ in this system, had 50 days instead of two to get acclimated to the hops and yeast, chew on it and digest it,” says Rynders. “Another advantage we found in the AnMBR was improved fouling control. The continuous pumping of the process wastewater into the tank provided cross-flow on the membranes, limiting surface fouling. We also used the biogas produced from the anaerobic digestion process to clean the membranes.” In all, the AnMBR system could run continuously for a few months without the membranes having to be cleaned.
Because of this longer digestion period and membrane efficiency, the team saw strong results in the quality of the AnMBR’s effluent, including a 98 to 99 percent chemical oxygen demand (COD) and biological oxygen demand (BOD) removal rate, as well as significant reductions in total suspended solids (TSS). By achieving such high-quality effluent output, the team demonstrated that the AnMBR system also added potential for water reuse. “Reusing this effluent to brew beer would require at least a disinfection process and possibly further advanced treatment,” said Rynders, “but even non-potable water could have many applications at a brewery and could significantly lower water-to-product ratios.”
In addition to meeting surcharge limits, the pilot study delivered a 98 percent recovery rate of methane biogas emitted by the digestion process, which could be used for heating or truck fleet fueling. “Biogas conditioning is one of the most interesting parts of this research,” says Rynders. “Every single brewer, livestock, dairy and food and beverage company should consider AnMBR, because the biogas production offers the potential to reduce capital investment paybacks and decrease fossil fuel dependence.”
One of the biggest appeals of R&D projects is that everyone is admitting they aren't the masters. That honesty is important.
Pushing the Limits
“One of the biggest appeals of R&D projects is that everyone is admitting they aren’t the masters,” says Rynders. “That honesty is important. It allows us to demand more from each other. For example, as we were testing the limits of the AnMBR approach, I told our GE partners we had to push the membranes to their breaking point, otherwise I hadn’t done my job. That’s not something they were used to hearing from an engineer!”
For Rynders, this project was a chance to expand his horizons. “I learned so much working on this project, feeling a different energy in a different industry. The speed and expectations were intense, so I had to become more agile. It opened up a new world of technical challenges and insights.”
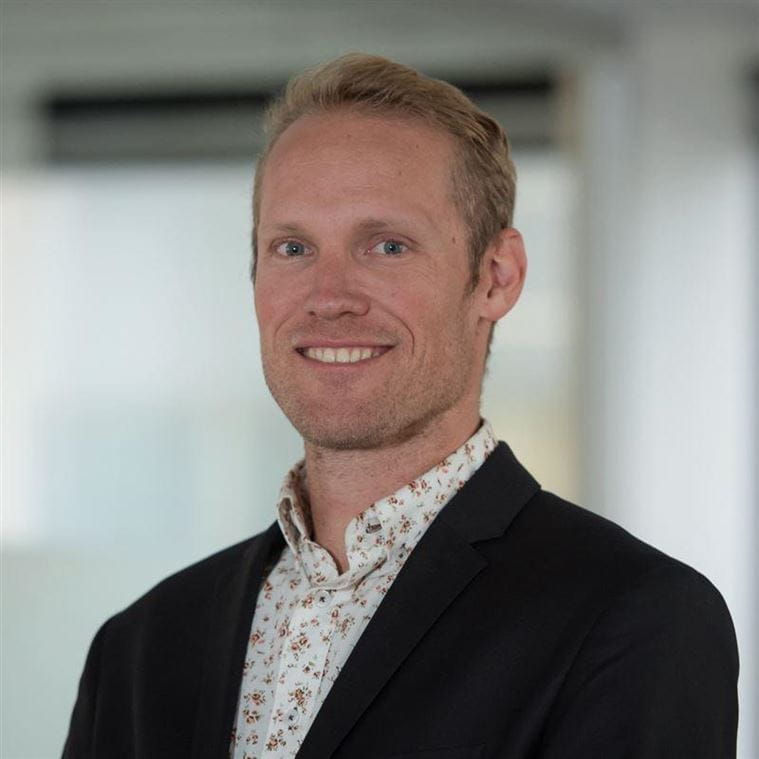
I learned so much working on this project, feeling a different energy in a different industry. It opened up a new world of technical challenges and insights.
Sign Up