The Intermittent Landfill Gas Reuse Option You Should Consider
Flaring is commonly used at landfills that don’t meet the typical beneficial landfill gas (LFG) reuse requirements. Depending on the proximity of a potential LFG user facility, as well as when and how often the LFG will be used, traditional methods of cleaning, dewatering, drying and delivering LFG may be deemed uneconomical. However, a simple, low-cost treatment solution does exist for intermittent LFG use.
Drawing out the Basics of LFG Treatment
In the past, LFG for intermittent uses would be considered a nuisance rather than as a viable resource due to the limited pool of potential users and the lack of a system to cost-effectively clean it to an acceptable quality. However, when thinking about the proper treatment for LFG and using standardized design components, a viable small-scale LFG treatment system for intermittent use is possible.
To treat LFG, you must remove moisture and particulate matter and create compression. These can be achieved by using readily available equipment and combining several systems to construct a master LFG treatment system. To achieve compression, you can easily adapt standard compressors and high pressure blowers, which have been used for many years to boost gas pressures, for use in a LFG situation. Filtration, used to remove particulate matter and moisture, is trickier. Historically, filtration required an expensive and complex chilling process for water removal. However, this process can now be completely replaced by using a consumable desiccant system.
Creating a Hands-Off Treatment Solution
The treatment process involves a dual vessel, two-type, consumable desiccant and filtration system so the LFG can be successfully compressed, treated and dried. The desiccants are contained in sealed vessels and react with the LFG to entrap and remove moisture. The resulting stream is drained from the bottom of each vessel either manually or continuously while they are in operation. Typically, each vessel is filled with desiccant at the beginning of a heating season or operational cycle and then operates unattended, except to check the desiccant levels through sight glasses on the vessels.
Cost savings are realized by using standard desiccant vessels.
The treated LFG can then be delivered through pipelines for use as a building space heating fuel or as a process fuel in nearby facilities. Since the heating load or process load at the facilities can be seasonal and/or cyclical, the LFG treatment system is designed for minimal capital costs, minimal maintenance, ease of startup and shutdown, and simplified, unattended operation.
Finding A New Market for LFG
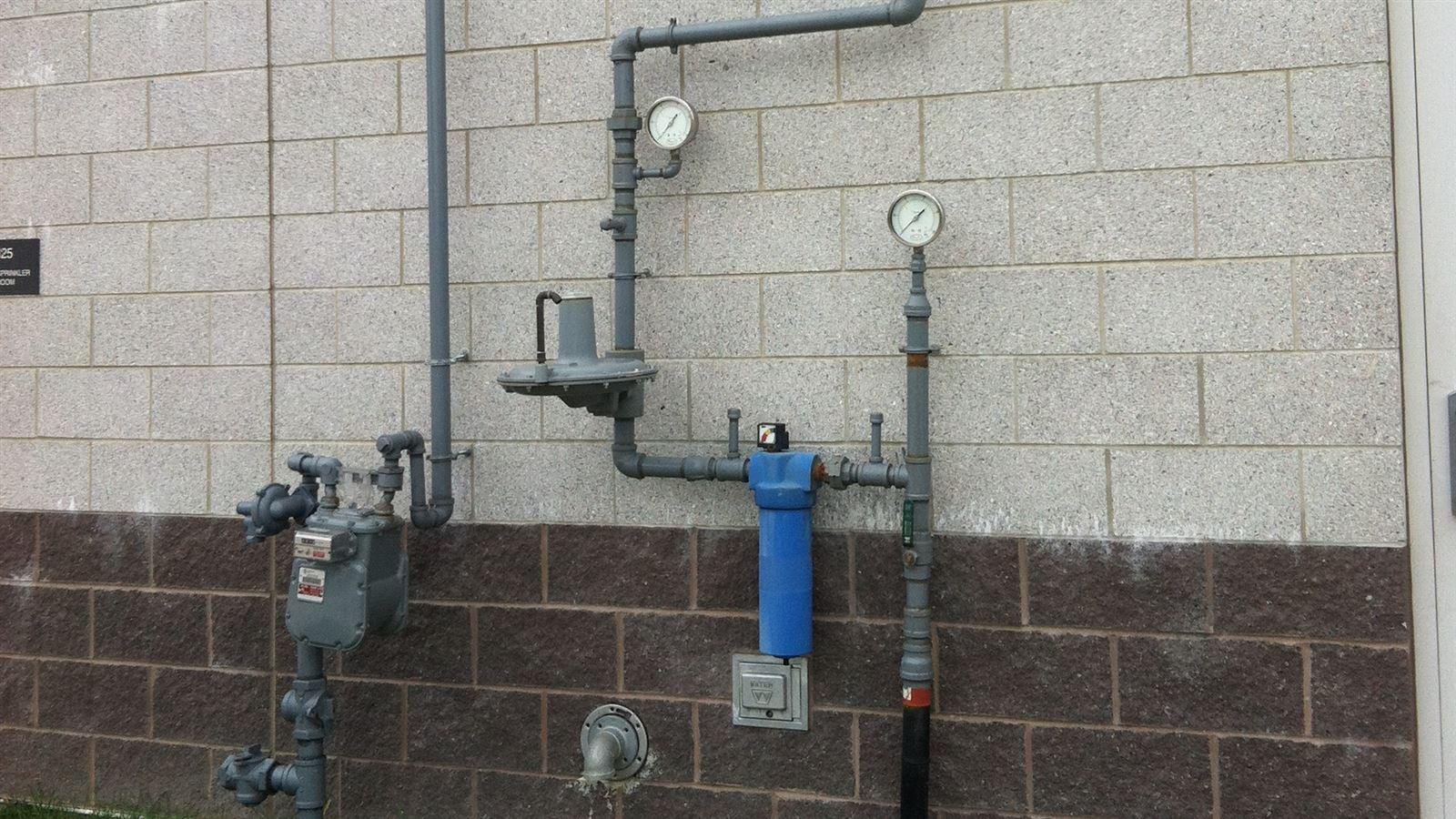
A system of desiccant drying and filtration can efficiently and cost effectively allow LFG to be used in a variety of applications. With standard, off-the-shelf components and straight forward system engineering, these systems can be assembled, delivered and placed into operation rapidly and cost effectively.
Joe Curro is a principal and senior solid waste engineer who leads CDM Smith’s landfill gas practice. His more than 45 years of experience in solid waste have concentrated on landfill gas, waste combustion and field operations. He has served as the lead design engineer for several projects involving landfill gas extraction, compression, flaring, beneficial use and transmission systems.
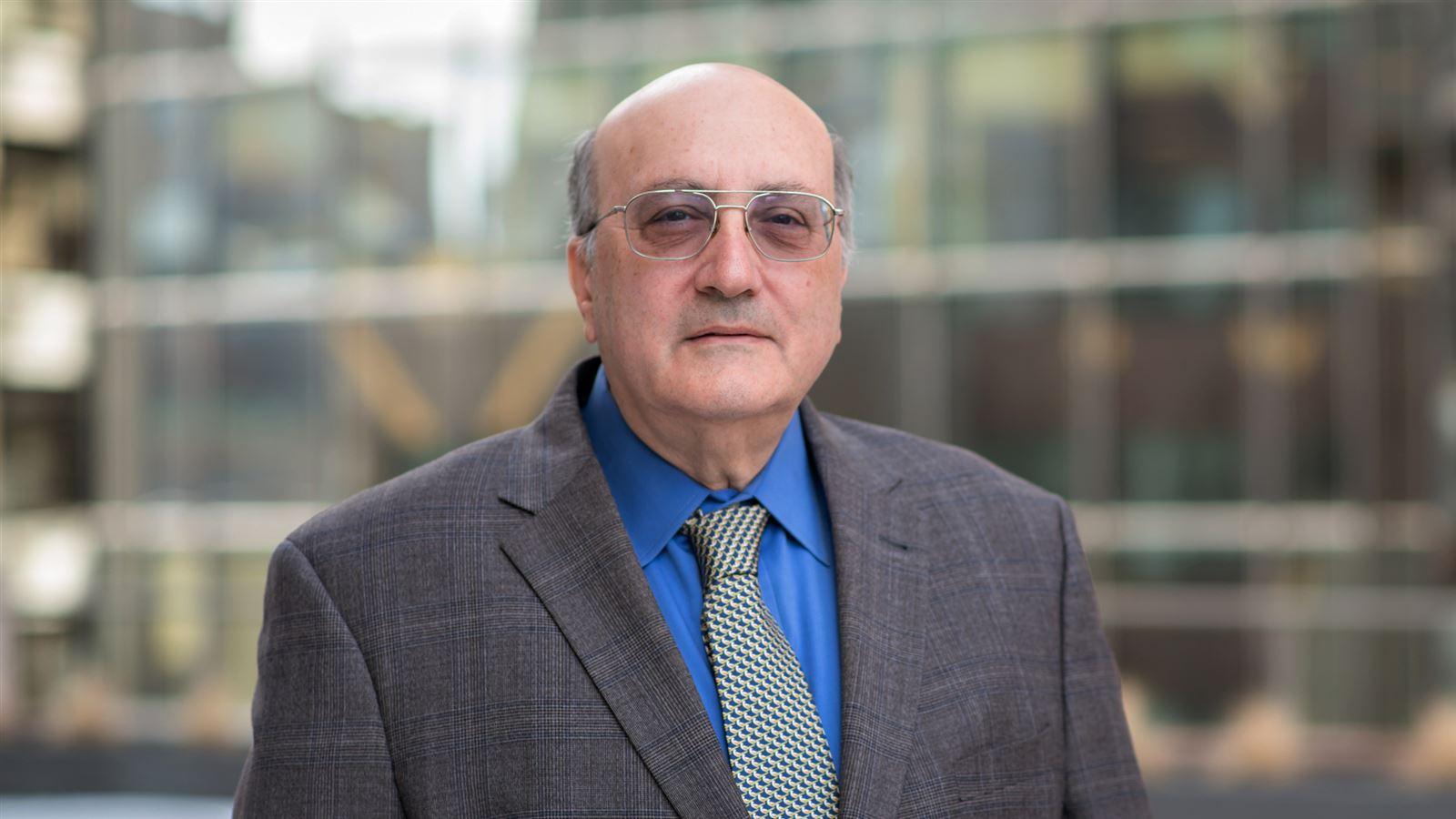
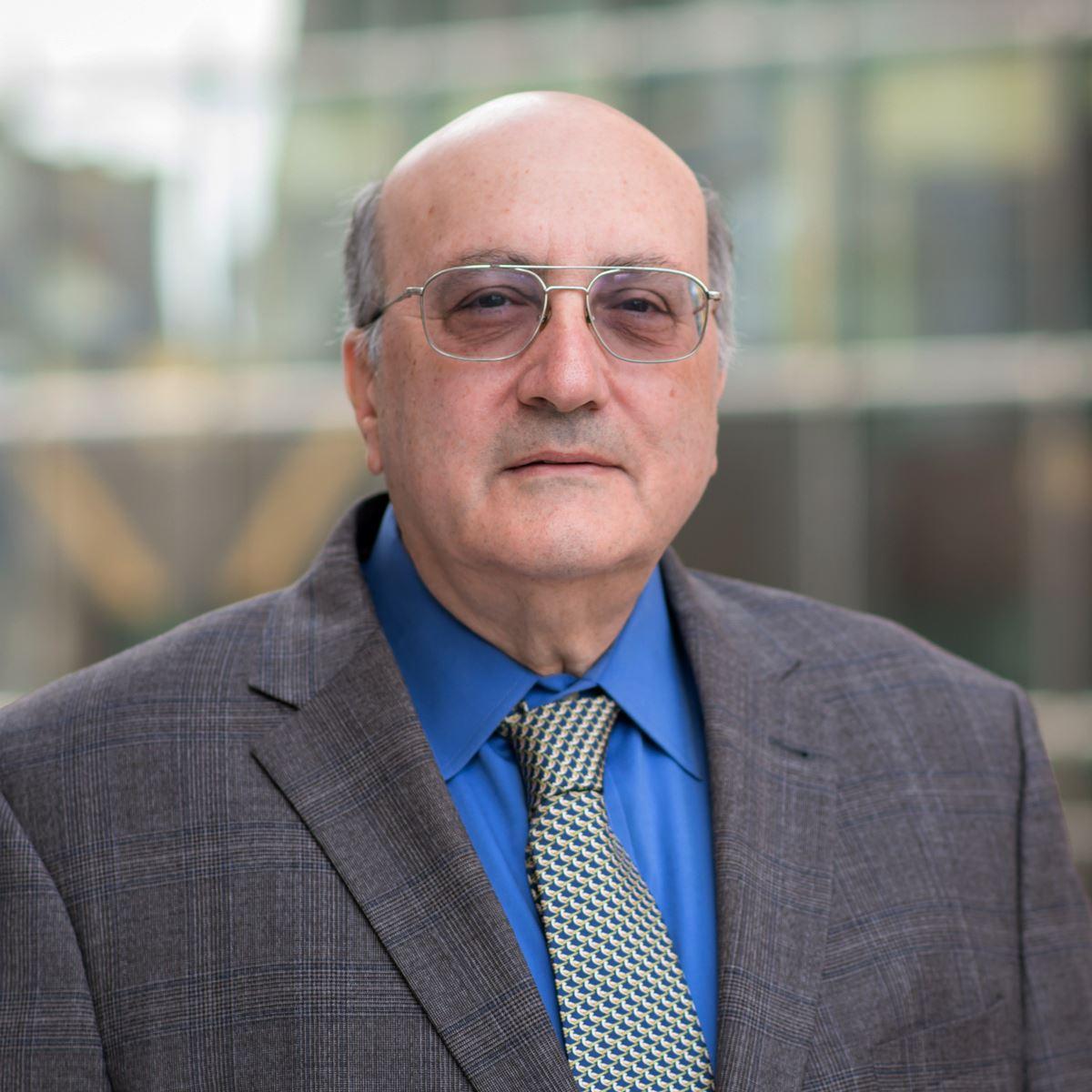
Cost savings are realized by using standard desiccant vessels.
