Planning a Successful LSLR Program
We polled three experienced civil and environmental engineers and construction managers from across the firm to gather tips and lessons learned on how to build a successful LSLR program strategy.
Taking action to comply with the LCRI
"The Lead and Copper Rule Improvements [LCRI] are making sure communities address their lead service lines head on,” Brian Kearney, seasoned lead service line replacement program manager explains. To comply with the EPA’s regulations, our experts recommend a few specific areas to focus on before the LCRI compliance date of November 1, 2027.
Most of the LCRI requirements will go into effect in 2027. However, utilities must use LCRR health effects language on materials and provide annual notifications in line with the LCRR to consumers with lead, GRR, or unknown lines annually each November in 2025, 2026, and 2027.
Between now and the “baseline” inventory deadline of November 1, 2027, it’s recommended that systems focus on reducing unknowns and begin replacements for LSLs with available Bipartisan Infrastructure Law (BIL) funding and other grants and loans. Consider that there will be a mandatory replacement requirement of LSLs in 10 years at 10%/year based on a rolling 3-year average starting on November 1, 2027 and your system will want to take actions before this to reduce the number of LSLs, GRRs and unknowns.
“We encourage our clients to not wait until 2027 to embark on the replacement process and anything they can do to reduce unknowns. BIL funding is available now and we don’t know what the future holds regarding additional funding. If you begin the replacement process in 2027 when it becomes mandatory, you’ll only have a couple of years to utilize available funding,” shares Sandy Kutzing, CDM Smith’s lead in drinking water task force leader. “Even if you don't have 100% of the information, you can conduct tests, perform inspections, and simultaneously use machine learning alongside your replacement plan. If you’re aware of service lines that need replacement, take advantage of the available funding. This applies especially to communities and systems with disadvantaged populations,” she adds.
Building a framework & making a plan
Identifying your constraints is a great starting point to roll out a successful LSLR program. Answering key questions will help provide a framework to inform the overall effort: How do you want to prioritize? Who needs to be involved? What are your constraints? How much do you want to spend per year? Do you want to establish a rolling program? Are you at risk for exceeding the action level? Is your program mandatory or voluntary for residents? Will the customers be charged for the replacement of the private side?
To avoid complications down the road, you want to make sure the public, local elected officials, politicians, any regulatory agencies at the state and local level, public works, municipal road programs, utility companies and other affected stakeholders are included or at least informed in the early stages of planning.
“The key to a successful lead service line replacement program is really on the planning side with logistics and data management; the actual work to replace a lead service line is fairly straightforward utilizing established trenchless technologies,” describes Brian Kearney.
Engaging the community
The primary objective of a lead service line replacement program (LSLRP) is to protect public health and a successful program requires community participation and public education. As Sandy Kutzing puts it, “you can’t have an effective program without community buy-in.” The community needs to understand why you’re doing this and how it benefits them—especially with certain components of the program like entering homes, digging holes in streets, and turning off water for the day, which can be disruptive but are critical for this work.
You can start building community trust when identifying unknown line materials. This could mean providing clear and immediate verification results after a physical inspections or conducting a self-verification marketing campaign, which empowers consumers to do something to help. Assigning extra customer service personnel to manage lead-related questions right after sending annual notifications helps customers feel heard and helped by water systems. Clear communication from the start makes it more likely the community will sign up for replacement when the time comes.
“Public outreach is critical because this project isn’t like a shiny new bridge—people can’t see it,” Brian Kearney shares. “It involves clean drinking water which people already expect. Community involvement helps get the word out to make sure the community understands the project, so that when the construction crews are on their block to do the replacement, residents know what's happening, they have their meter accessible and they're letting the contractors in to get the work done with minimal disturbance.”
Choosing the right tools
It’s helpful to set up a data management system that can communicate with other tools you’ll be using such as construction management software. We recommend it being flexible enough to make changes as you proceed. Having program management software with geographic information systems (GIS) capabilities to capture and share project data—from existing public records and pre- and post-construction photos, to resident information and sampling results—will help effectively manage the program and streamline reporting and communication requirements. Storing all of the information in one place will make sure your team is organized and can access resources efficiently and help minimize errors.
“GIS can be used to predict length of service lines,” shares Colleen Heath, a distribution expert who has worked on several small-scale programs in New England. “It can be used to create maps showing other municipal projects in the area to create efficiencies during construction and can be exported into Excel to expedite the repetitive process of tracking replacements.”
Because there are so many moving parts to a LSLRP, it’s crucial to manage and track data in a way that’s efficient, accurate and accessible. Programs that store information like inventories, sampling results, replacements and communication with residents can elevate how you manage your program’s data. Trinnex’s leadCAST is a tool you can use in conjunction with GIS to maintain compliance with the latest regulations, ensuring that nothing falls through the cracks. leadCAST is the only platform that connects inventory management with construction management tools for tracking replacements, which can support water systems in their march to get the lead out and protect public health.
Although EPA has recognized the use of machine learning, it is ultimately the individual state’s decision on whether or not to approve it for assigning materials to service lines. "Any utility that has a significant number of unknowns in their service line inventory can take advantage of predictive modeling and we can work to help obtain state approval,” advises Trinnex data analyst Katie Deheer.
Using machine learning enhances material classification, streamlines field verifications, and prioritizes program efforts to save utilities time and money. Katie’s team of data scientists has developed a predictive modeling tool called leadCAST Predict to help water systems meet LCRI requirements while protecting public health.
Our experts suspect with the LCRI, that state regulatory agencies will feel more comfortable using alternative methods because of the additional non-lead validation steps that will now be required. Our experts advise that the validation step was likely added to address concerns with machine learning and other methods where you don’t physically see the wall of the pipe. The non-lead validation pool provides a second check on the service lines classified as “non-lead” by the end of 2034. Contact CDM Smith to learn more about how to set up your inventory for the non-lead validation pool.
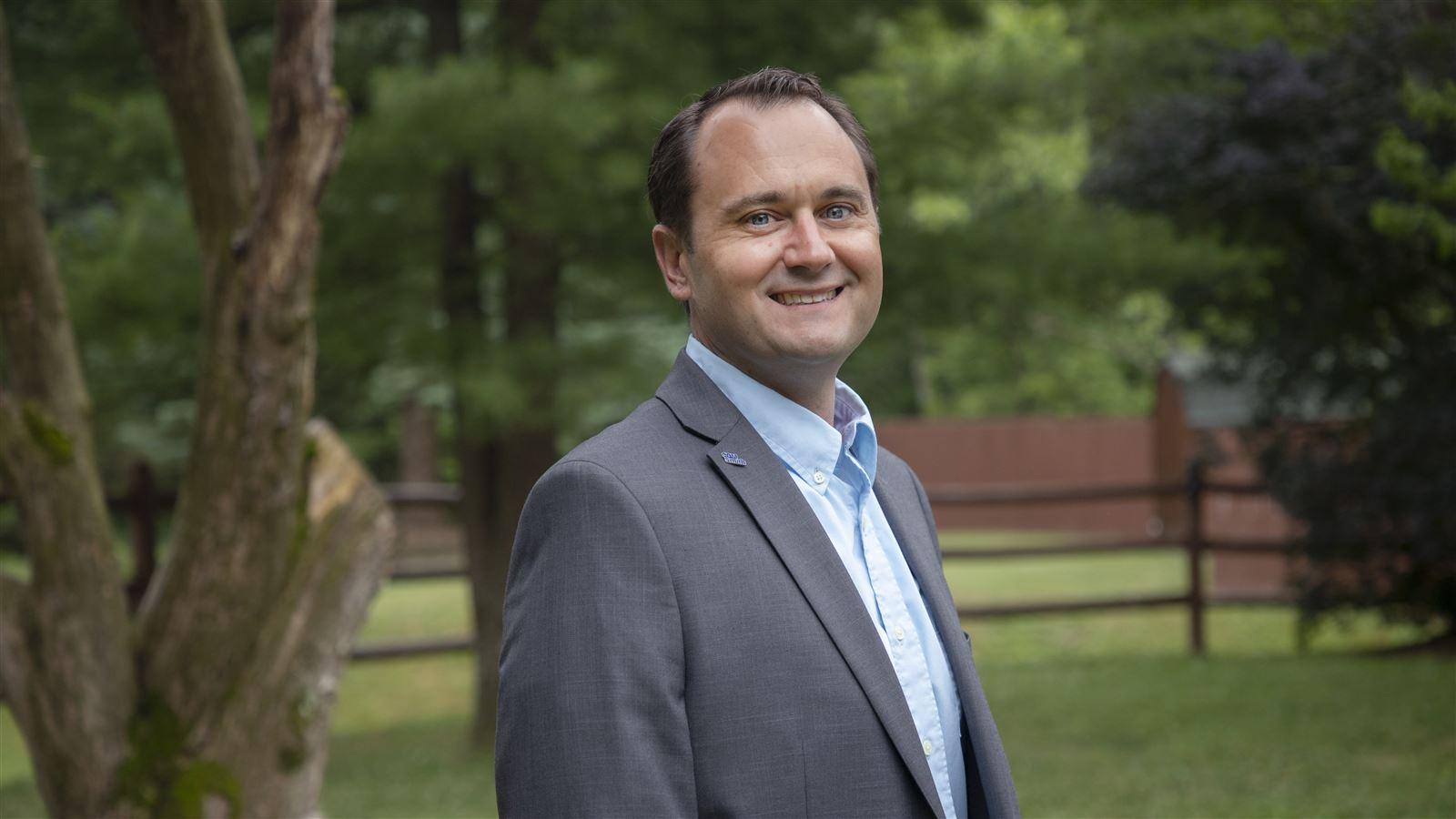
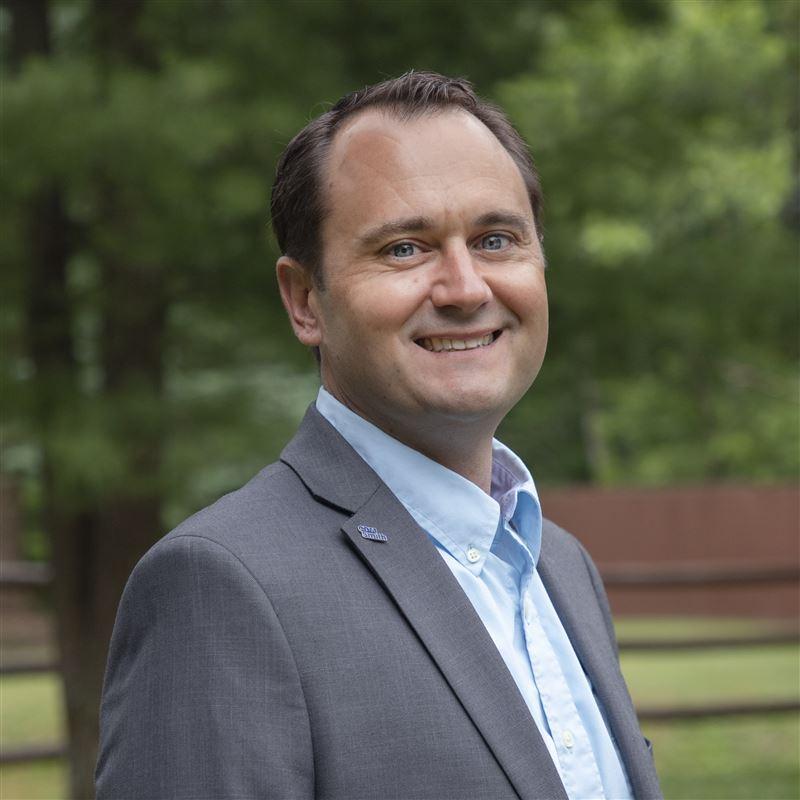
The Lead and Copper Rule Improvements are making sure communities address their lead service lines head on.
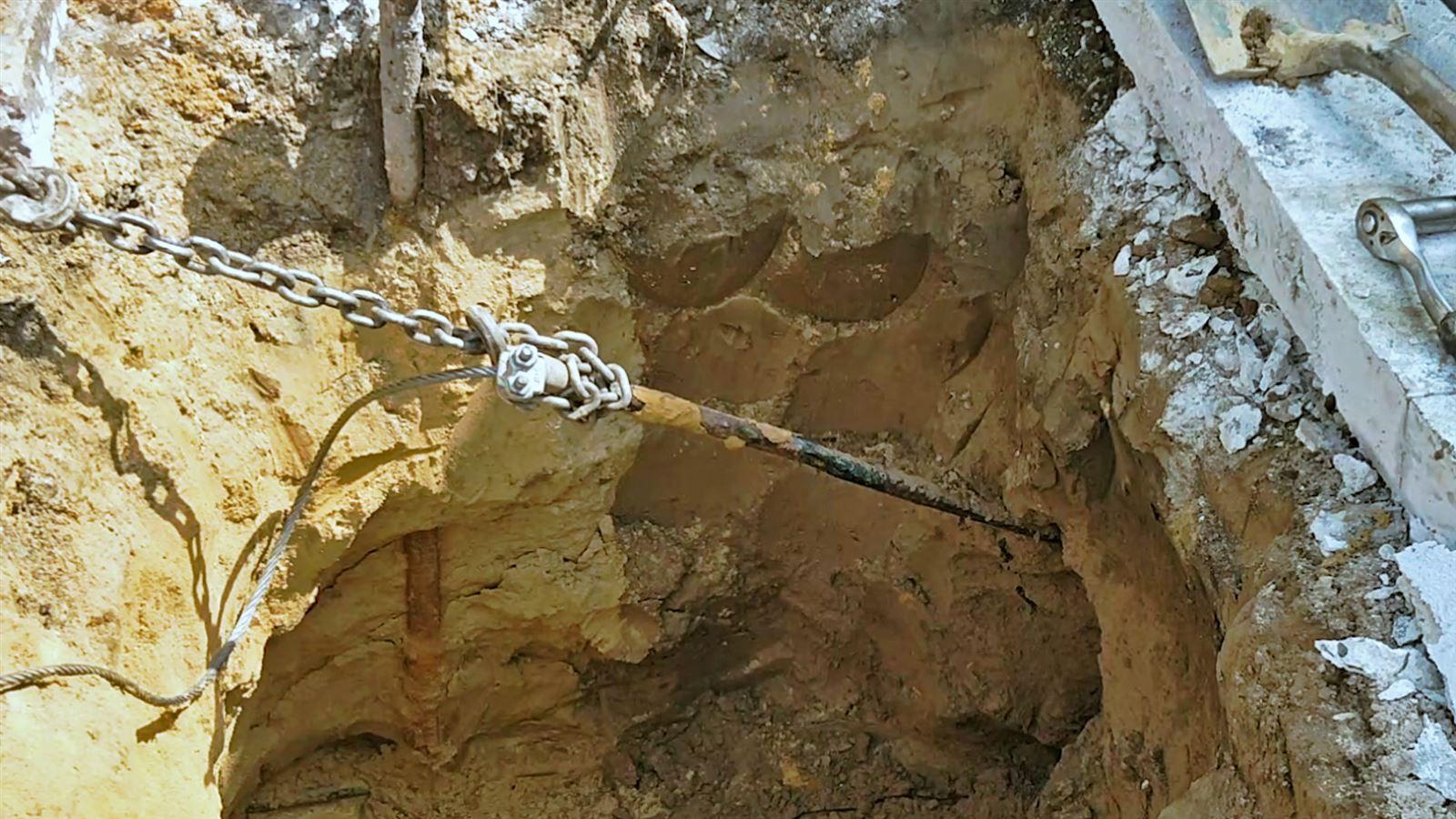
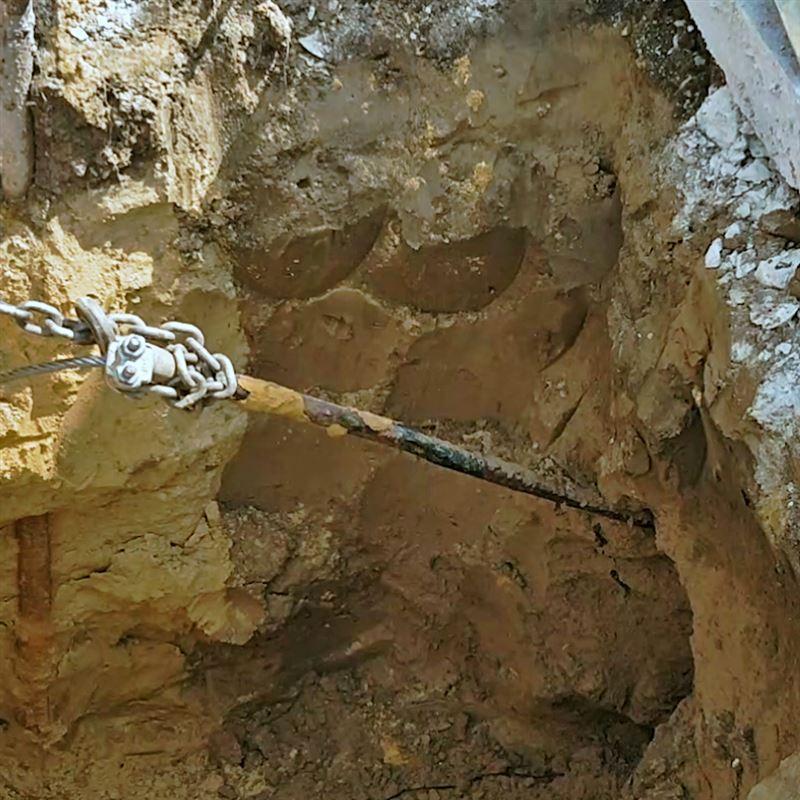