Water and Force Main Rehabilitation: Your Options
In our recent on-demand webinar, “Water and Force Main Rehabilitation,” Cindy Preuss and Brent Johnson presented eight relevant technologies. Here we define these options for water and force main rehabilitation and describe the benefits and drawbacks of each option.
What are my options?
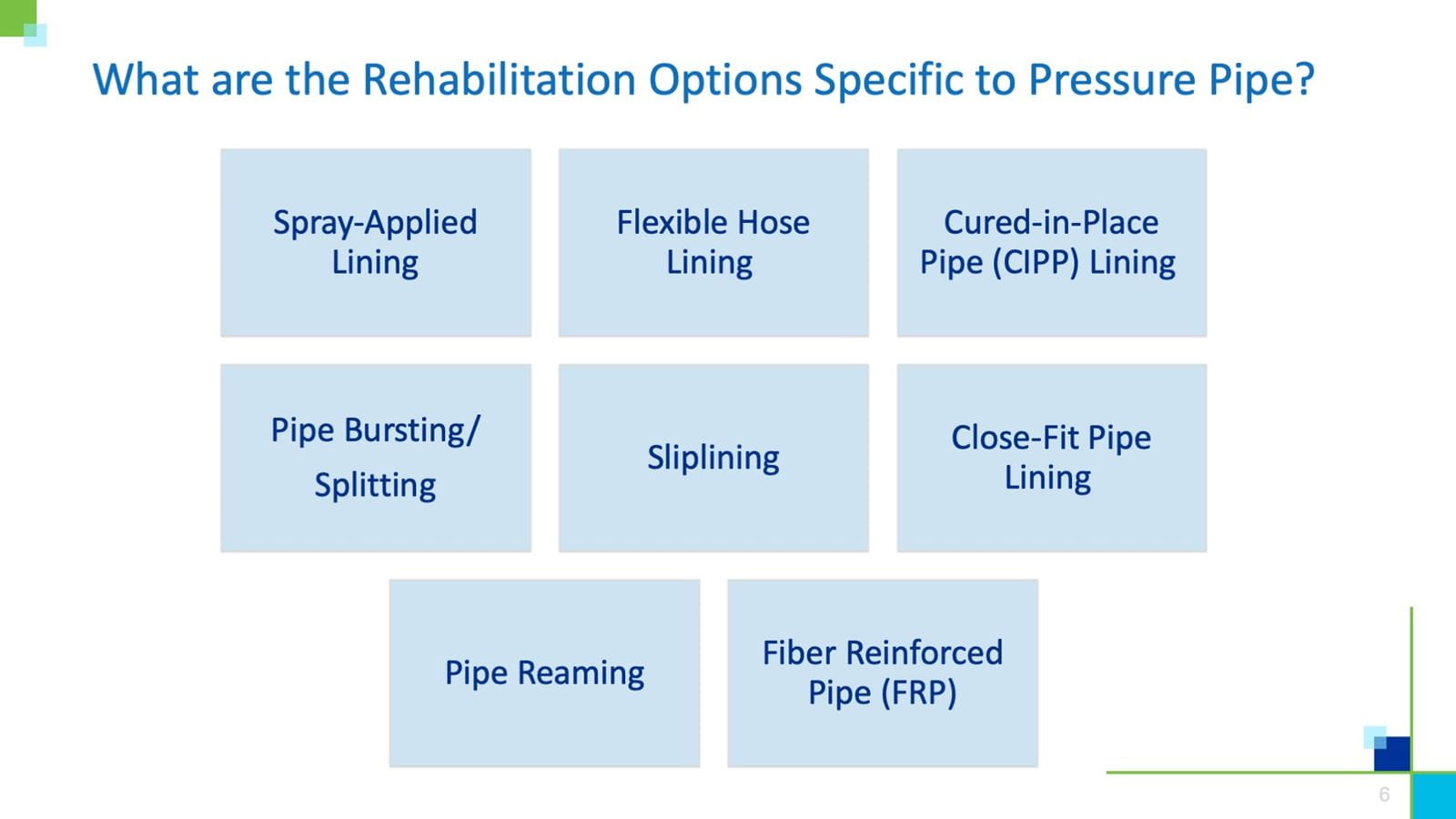
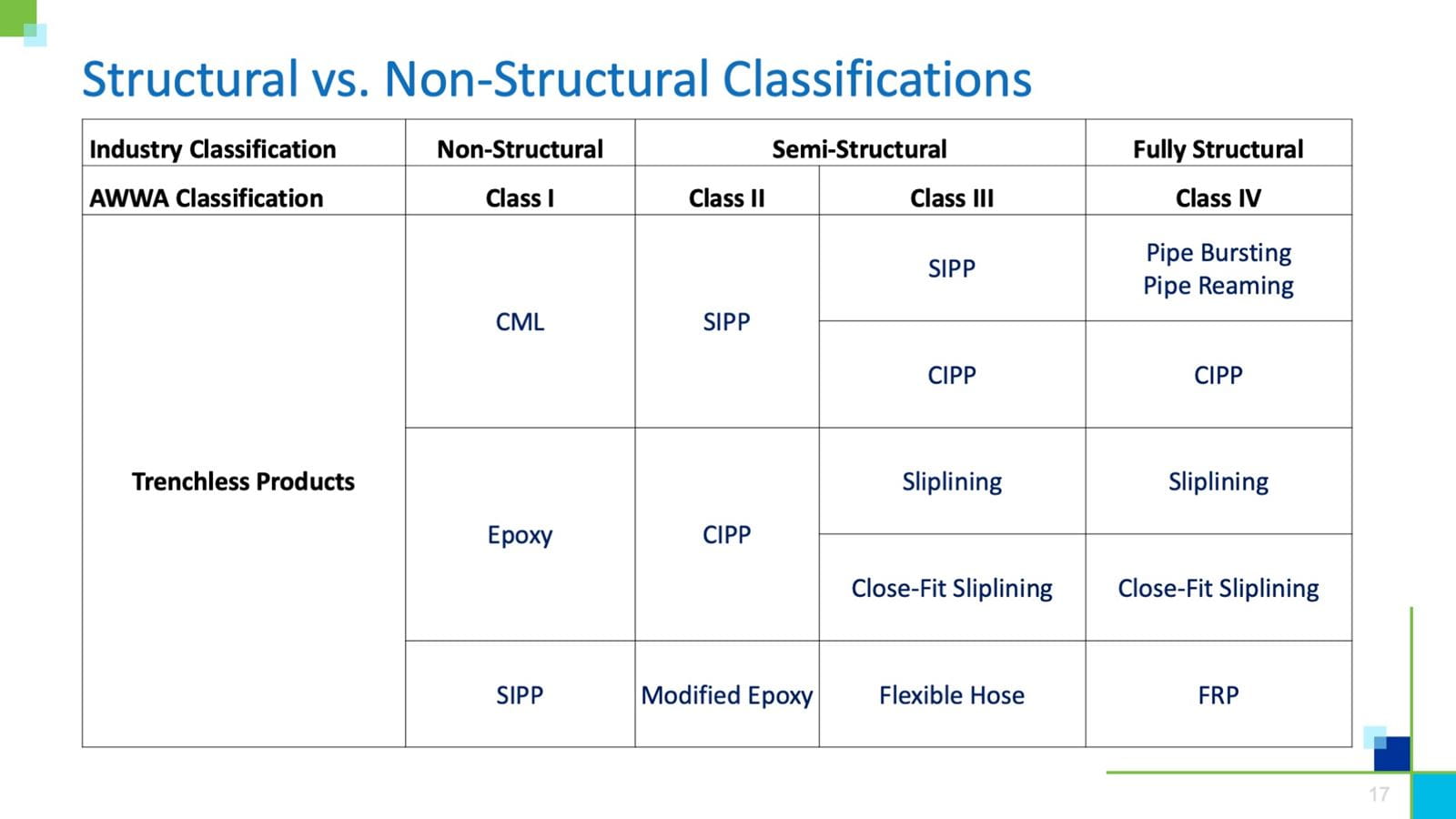
Spray-Applied Lining
There are different product categories for spray-applied lining, a nonstructural or semi structural solution that ranges from class I to class III. These product categories include cement mortar lining (CML), epoxy lining, and spray in place pipe (SIPP).
Some of the benefits of spray applied lining systems are improved water quality, minimal loss of internal diameter, handles large range of diameters, and service connections do not have to be excavated to return to service. Some of the drawbacks of a spray applied lining system are that it is non- or semi-structural only, it can crack under load bearing applications, it requires a completely cleaned and dewatered pipe, valves and elbows must be removed, and it requires a round pipe.
Flexible Hose Lining
Flexible hose lining, also referred to as flexible fabric reinforcing pipe (FFRP), is a high strength rehabilitation technology that requires a constant pressure. There are a couple types of applications for FFRP, such as pull in place, very small excavations, and it can navigate elbows. The technical envelope for FFRP is up to 20” diameter installations. This technology has a very high coefficient of friction (C=150), and some significant lining lengths that are limited essentially by appurtenances; they can be up to 8200 LF smaller diameters, and approximately 1 mile for a 20" diameter pipeline.
Some of the benefits of FFRP are that it can navigate back-to-back (or stacked) elbows, it can do an acute 90-degree angle, and it is a good candidate technology for quick return-to-service. The drawbacks of FFRP are that there needs to be constant pressure and that future taps and repairs require spool pieces.
Cured-in-Place Pipe (CIPP) Lining
CIPP is a semi or fully structural, class III or IV solution technology, and it consists of a reinforced felt or woven polyester fiber hose, that is impregnated with epoxy or vinyl ester thermosetting resin. With this technology, a liner is inverted into the host main using water or air pressure, and then cured with hot water or steam. Typically, with water and force main rehabilitation, valves and fittings govern project install lengths; CIPP can typically line through up to 45-degree bends, as well as line through gate valves that are non-functioning, or need to be abandoned.
Some of the benefits of CIPP are that there are both full- or semi-structural options, installation is rapid, there is minimal loss of internal diameter, and it can handle some bends and a large range of diameters. The drawbacks of CIPP are that pressure testing can be problematic, as ends must be sealed to keep water pressure from getting behind liners, or liners can have manufacturing defects.
Pipe Bursting/Splitting
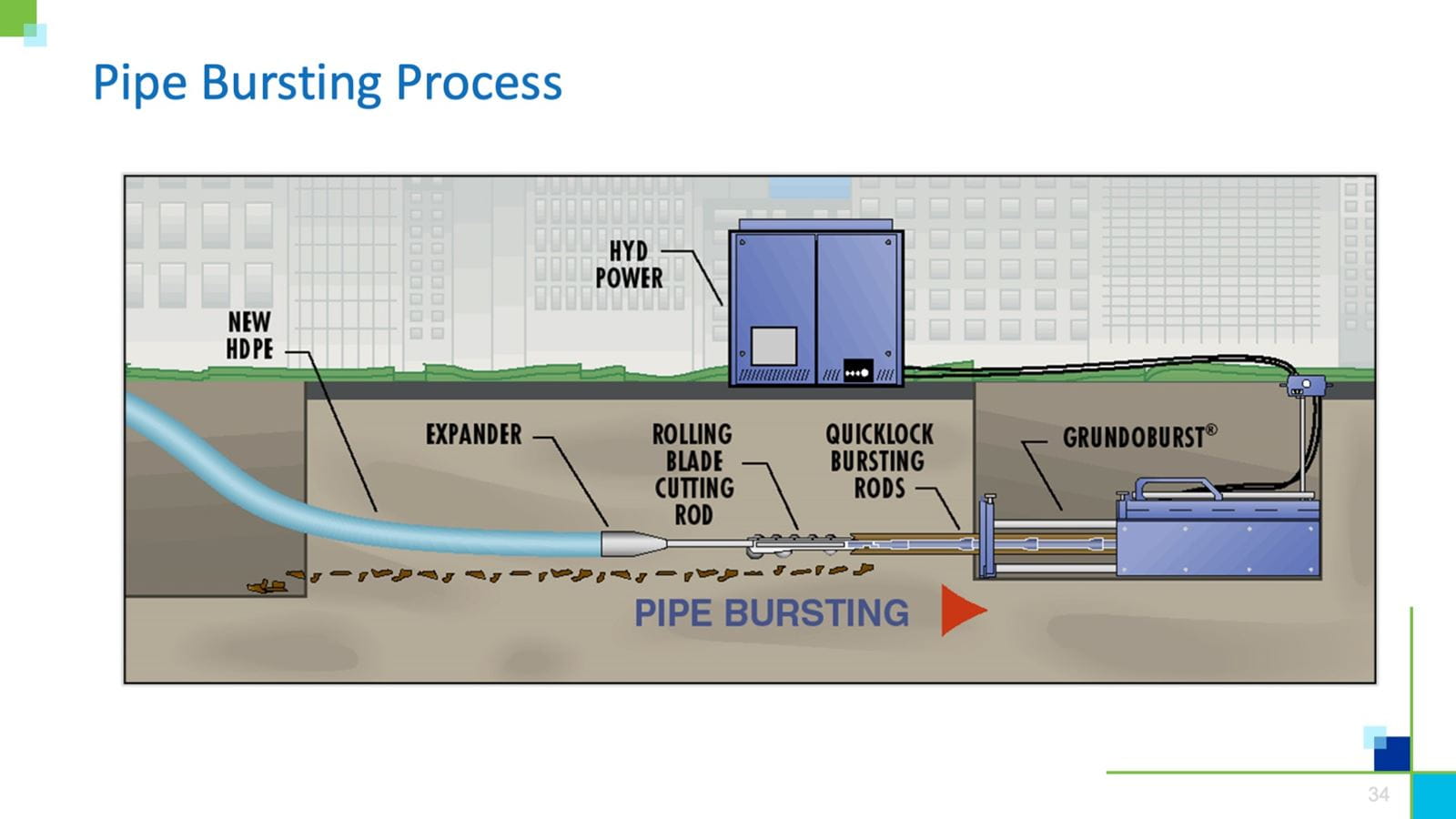
Whether it is considered pipe “bursting” or pipe “splitting” depends on the pipe’s material. Pipe bursting is for fractural pipes, whereas more flexible material pipes are cut or split open. This technology requires access pits on both ends. There are two pipe bursting methods unique to water mains, which include pre-chlorinated and micro pipe bursting.
One of the benefits of pipe bursting or splitting is that it is your only option if you need to upsize your main. One of the drawbacks is that excavation is required for access pits and appurtenances (valves, fittings, services, and repair clamps). Additionally, the expander heads have the potential to create “pressure bulbs,” which can affect nearby utilities, like sewer mains, storm drains, and other water mains. Other drawbacks are that it is possible to heave or slump the roadway if you don’t have enough depth to accommodate displaced soils, and changes in pipe material along a given length must be identified to outfit cutters to handle the varying materials.
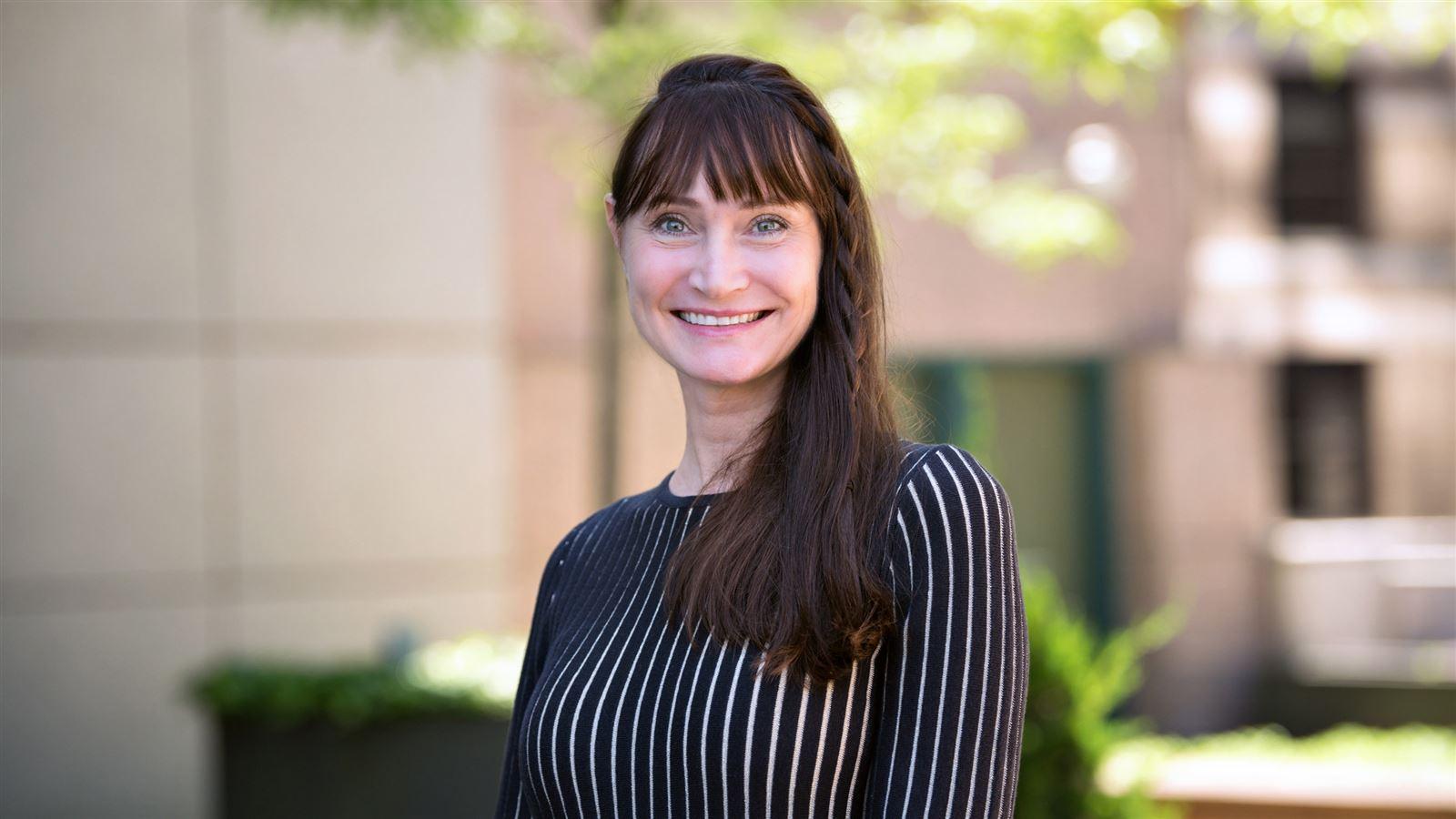
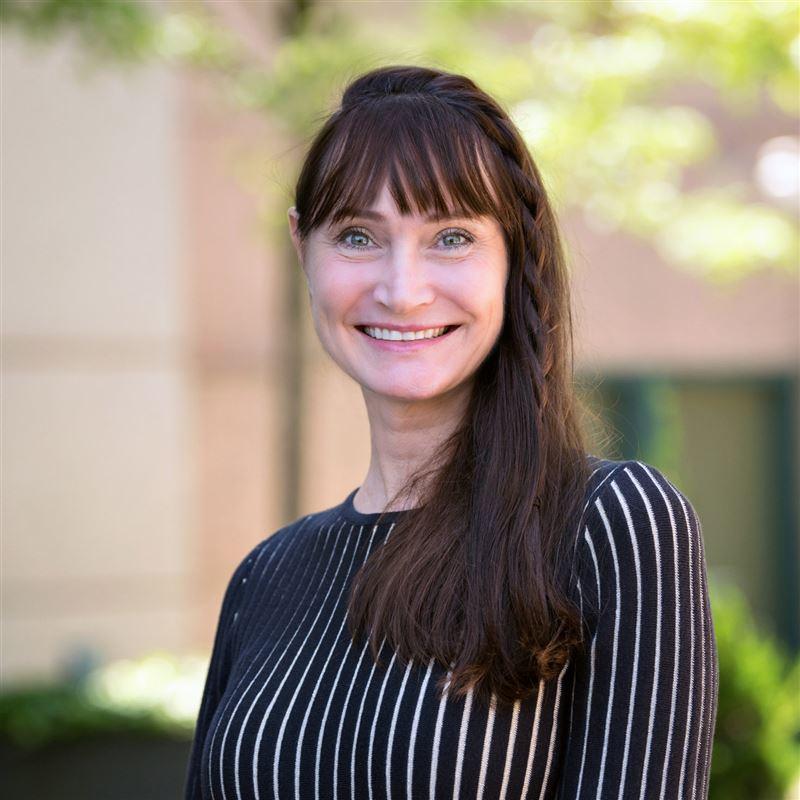
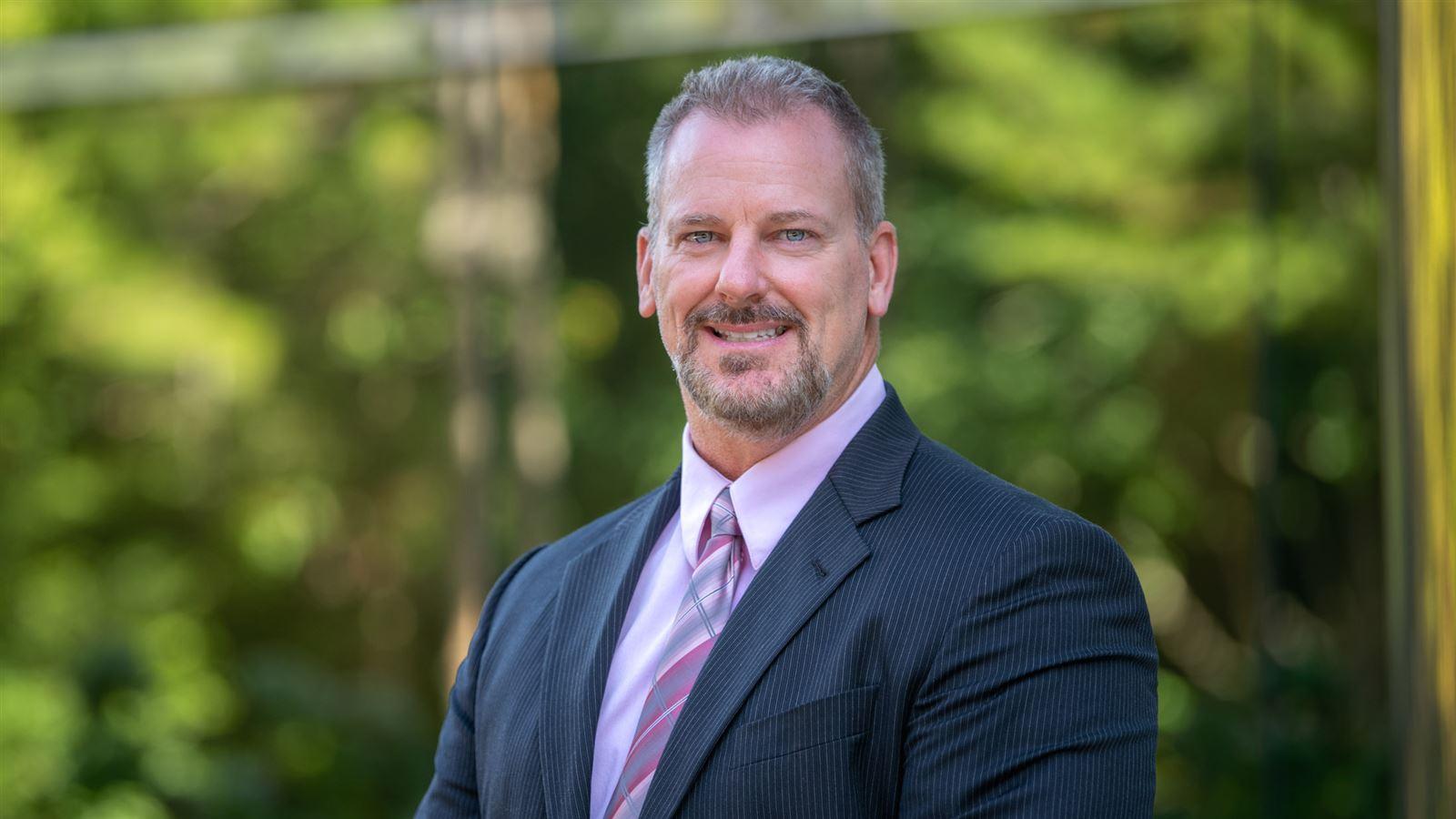
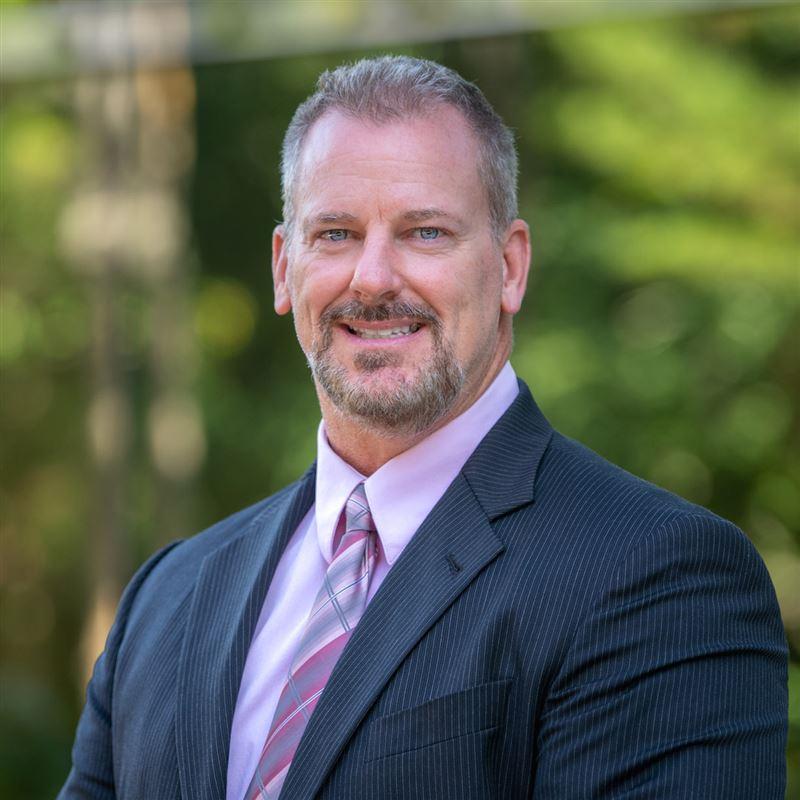
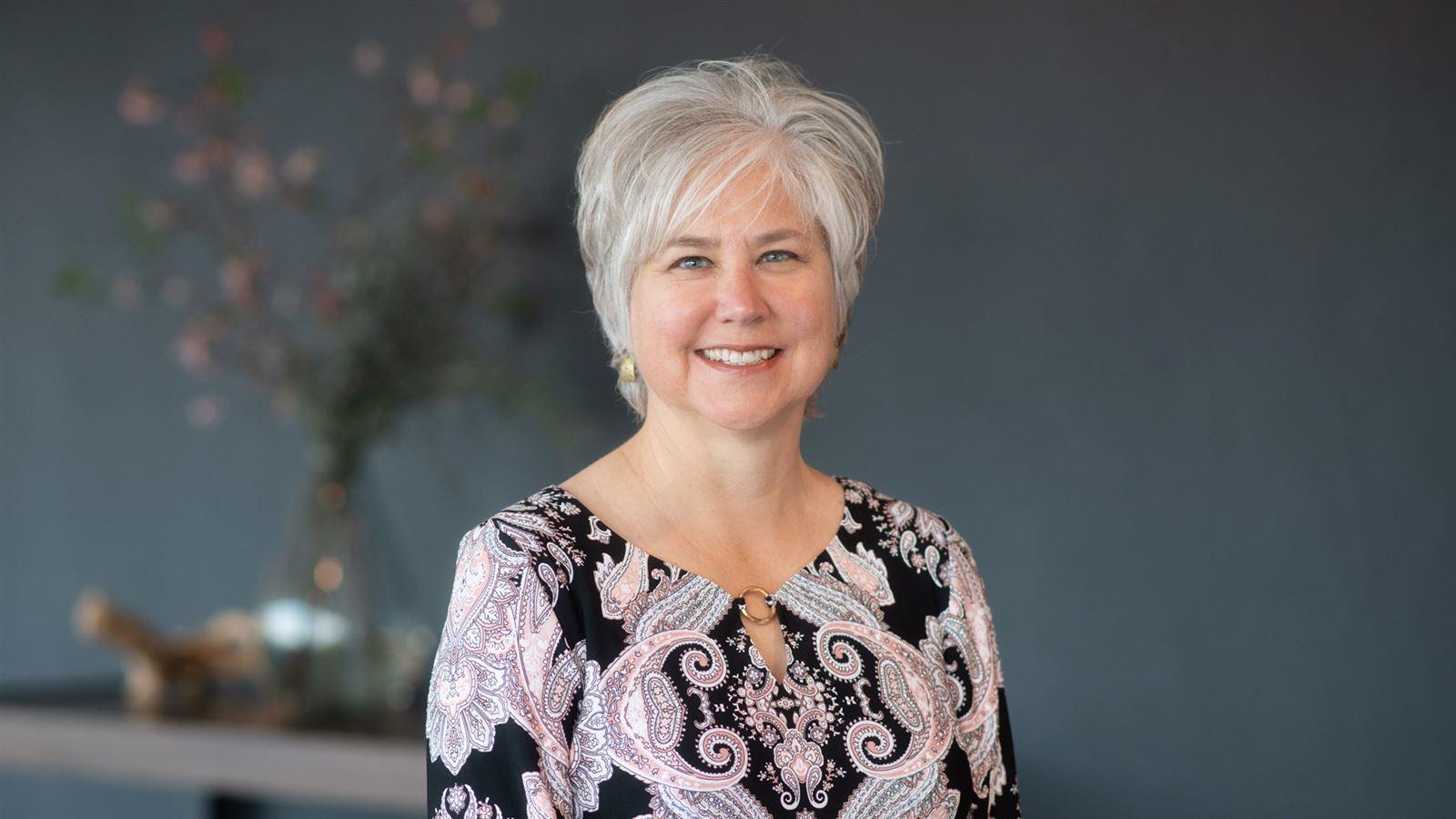
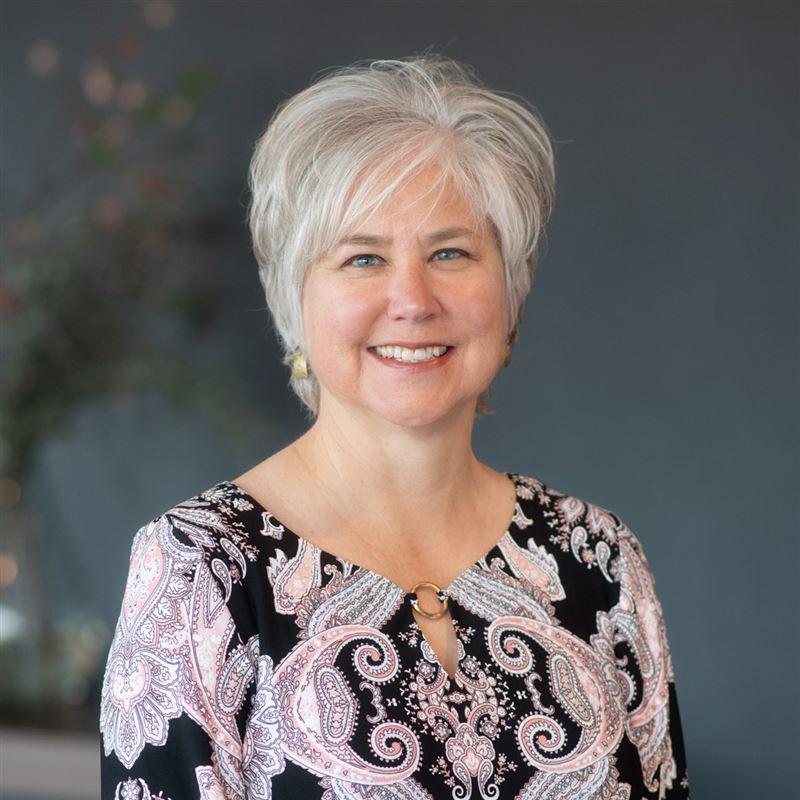
Sliplining
The oldest of all the rehabilitation technologies, sliplining, involves a new pipe being pulled or pushed into an existing, larger diameter host pipe. Common lining materials are Fusible PVC and HDPE, as plastic materials are flexible which aid in installation for long runs, and give improved coefficients of friction. In this process, you must CCTV the main, clean as needed, conduct proof (or mandrel) testing, get the pipe string ready, do the insertion, conduct pressure testing, and lastly, grout the annular space.
Some of the benefits of sliplining are that it is rapid and works for many pipe materials like PVC, HDPE, and CCFRMP. One of the drawbacks of sliplining is that valves, tees, and elbows, as well as services, must be excavated for reconnections, requiring multiple pits. Additionally, slipline pipe diameters must be smaller than the host pipe in order to pull/push the pipe in place, resulting in a reduced capacity as well as a need for grouting of the annular space.
Close-Fit Pipe Lining
To offset the loss of capacity of traditional sliplining, some closer fit sliplining options have been developed. Deformed or reformed systems--close-fit lining systems—include systems like Swagelining, rolldown, and compact pipe. These systems temporarily reduce the diameter of the plastic slipline pipe strings for installation into the host pipe, after which the pipe expands into place fitting snug against the inside diameter of the host pipe. This takes specialized equipment, is less common, and is more expensive.
Some of benefits of close-fit lining are that it is rapid, there is a minimal loss of internal diameter, no grouting is required, and it can handle bends of up to 45-degrees. One of the drawbacks is the reversion process from the pipe’s reduced diameter to full diameter, which must be complete before connections are made and services reinstated. If the reversion is not completed the liner could move and pull away either from end, side, and/or service connections, as well as appurtenant connections. Thus, it is mainly only applicable to smaller diameter pipes, usually 12 inches or less.
Pipe Reaming
Pipe reaming is a cross between horizontal directional drilling (HDD) and pipe bursting. It is different from pipe bursting in the sense that it does not create a pressure bulb from the expander head and pieces of existing pipe pushed outward along the alignment. Instead, soils and existing pipe spoils are vacuumed out of the hole during reaming, leaving a clear, open conduit for insertion of the new pipe behind the reaming head.
Some of the benefits of pipe reaming are that surrounding conditions (groundwater, sand, rock, concrete encasement) that prohibit other procedures are less of an obstacle, and this technology can handle shallow depths. Some of the drawbacks of pipeline reaming are that it is limited to non-metallic pipeline replacement, may not be performed on asbestos cement pipe, and it has a 20 to 30 percent higher cost.
Fiber Reinforced Pipe (FRP)
Fiber reinforced pipe (FRP) is a polymer (epoxy, vinyl-ester, or polyester) reinforced with fiber (carbon, glass, Kevlar, basalt, etc.), applied either on the interior or exterior of the pipeline.
Some of the benefits of FRP are that it accommodates significant increases in pressure ratings, has a very small footprint, and produces a minimal increase in wall thickness (typically ¼ inch (5mm)). Thus, it is ideal for maintaining flow capacity for the pipe, and it is also ideal for spot repair of damaged areas. Some of the drawbacks of FRP are that is has a high cost and it requires specialty installation.
To learn more about these technologies in depth, watch our on-demand webinar.